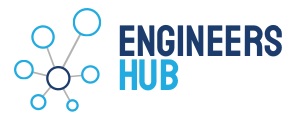
Technologie des élastomères
Cette page explique les termes clés utilisés pour définir les propriétés des élastomères.
Propriétés chimiques
Tous les types d’élastomères sont susceptibles aux attaques chimiques de divers niveaux. La compatibilité d’un caoutchouc dans un environnement particulier dépend à la fois de la structure du polymère et de la façon dont il a été formulé.Une incompatibilité chimique peut avoir divers effets sur le composant en caoutchouc, en fonction de la nature exacte de l’attaque chimique, les effets étant amplifiés ou accélérés à des températures élevées. Les effets physiques peuvent être :
- Fragilisation et durcissement
- Ramollissement et état collant
- Gonflement
- Perte de volume
Les effets les plus courants sont le gonflement, en raison d’un effet de solubilité ou d’une attaque chimique entraînant la modification de la polarité de l’élastomère. Bien que l’augmentation de volume soit réversible, les effets sur le polymère ne le sont pas.
La fragilisation et le durcissement sont révélateurs d’une réticulation accrue, un ramollissement indique une dégradation du réseau du polymère/de la réticulation. Une perte de volume est le plus souvent liée à l’extraction des plastifiants et des adjuvants, ce qui donne un matériau moins flexible.
Coefficient de dilatation thermique
Tous les matériaux (à quelques exceptions prés) se dilatent lorsque la température augmente. Le degré de dilatation est caractéristique du matériau. La valeur est exprimée en termes de dilatation linéaire ou volumétrique qui se produit avec chaque unité de longueur ou de volume pour chaque degré d’augmentation de la température.
Propriétés de compression
- Déformation rémanente après compression - Une mesure de l’élasticité du matériau après une action prolongée de compression soit à température ambiante soit pendant l'exposition à des températures élevées. La déformation rémanente après compression est souvent utilisée comme mesure de l’état du durcissement ou de la force de réticulation ; elle est mentionnée en détail dans les applications d’étanchéité pour mettre en relation les caractéristiques du matériau et la prévention des fuites, lorsque la récupération de la forme du joint est nécessaire après déformation.Les changements physiques et chimiques pouvant survenir sur un élastomère à des températures élevées peuvent empêcher l'élastomère de retrouver complètement sa forme d’origine après suppression de la contrainte de compression. Le résultat est connu sous le nom de « déformation rémanente après compression » et correspond au pourcentage de perte de forme par rapport aux dimensions d’origine.ASTM D395 définit deux méthodes de test différentes (A et B).La méthode A n’est pas souvent mentionnée, mais elle concerne une charge constante.La méthode B est la méthode la plus couramment utilisée où un échantillon de dimensions spécifiques est comprimé jusqu’à une flexion définie ; après une exposition à des températures élevées, l’échantillon est retiré du dispositif de flexion et on le laisse reposer à température ambiante avant de mesurer les dimensions finales. Une variante de ce test moins couramment utilisée est mentionnée dans la norme ISO 815, où on laisse refroidir les échantillons lorsqu’ils sont toujours sous compression.
- Relaxation de la contrainte de compression - Les élastomères sont des matériaux viscoélastiques qui se comportent essentiellement à la fois comme un solide élastique et un liquide visqueux. Une déformation constante d’un élastomère peut entraîner des changements dans sa structure interne, qui peuvent à leur tour modifier les caractéristiques contrainte-déformation du matériau sous charge.Lorsqu’il est comprimé, de l’énergie est à la fois stockée et dissipée par le matériau, c’est-à-dire que les deux effets, à la fois élastiques et visqueux, se produisent.Par conséquent, lorsque l’élastomère est comprimé, il génère une force de réaction (ou « force d’étanchéité »). Cependant, avec le temps, l’énergie stockée diminue, ce qui réduit la force d’étanchéité initiale. Cette diminution de la force d’étanchéité est connue sous le nom de « relaxation des contraintes en compression » (CSR) La CSR est parfois appelée force d’étanchéité retenue dans le secteur des joints et des garnitures. Le phénomène peut être accéléré par l’exposition à des produits chimiques et/ou à des températures élevées qui attaquent le squelette du polymère ou le système de réticulation.La CSR est mesurée en comprimant une éprouvette standard avec une contrainte constante et en mesurant la force exercée par l’éprouvette à des intervalles définis dans des conditions spécifiques. La force décroissante est exprimée en pourcentage de la contreforce initiale.
- Module d‘élasticité en compression - Le module d’élasticité en compression est une propriété physique importante des élastomères qui détermine la quantité de contrainte qu’un matériau présente pour une quantité donnée de contrainte de compression.L’essai est parfois appelé essai de « flexion en charge ».Les résultats du test dépendent beaucoup des dimensions de l’éprouvette en raison de l’effet « facteur de forme » lors du test d’
élastomères. Le « facteur de forme » est le rapport entre la surface de l’éprouvette et la surface de l’éprouvette « sans bombement » ;
il est à noter qu’un échantillon avec une surface importante, mais une petite surface sans bombement, présente une augmentation rapide du module.
Décompression explosive
La perméabilité d’un gaz dans un élastomère sous haute pression peut ne pas avoir d’effet à long terme à condition que la pression soit relâchée graduellement, permettant ainsi au gaz de s’échapper de l’élastomère. Cependant, si la pression est relâchée rapidement, le gaz sous pression peut se détendre brusquement, rompant l’élastomère de manière catastrophique. Des composants en élastomère spécifiques sont nécessaires pour éliminer cet effet, les matériaux formulés ayant tendance à être très durs. Voir page 8 pour obtenir des informations sur les essais de décompression explosive.
Friction, usure et abrasion
La résistance à l’usure d’un caoutchouc lorsque sa surface est soumise à une action mécanique. Elle est généralement exprimée comme un indice de résistance à l’abrasion en se référant à un caoutchouc standard et elle s’applique à toutes les méthodes.
- Friction - La friction peut être définie comme étant la résistance au glissement d’un matériau sur un autre. Les essais de friction concernant les élastomères sont principalement associés à l’industrie des pneumatiques et peuvent être divisés en deux catégories distinctes : statiques et dynamiques. Les essais sont généralement réalisés en utilisant un « traîneau » de matériau chargé avec des poids supplémentaires pour produire une charge normale. Ce traîneau est ensuite glissé sur une surface dont la finition est connue. La force de résistance résultante peut être rattachée au coefficient de friction (μ) en utilisant la formule F = μR, où F est la force de résistance et R est la force normale. Cette méthode présente un grand nombre d’inconvénients, car les élastomères ne se conforment pas complètement à cette équation, les données peuvent toutefois être comparées.
- Indice de résistance à l’abrasion - L’expression de la résistance à l’abrasion, qui est le rapport entre la perte de volume d’un caoutchouc standard et la perte de volume du caoutchouc testé, déterminé dans les mêmes conditions spécifiées et exprimé en pourcentage. L’essai consiste à érafler le caoutchouc à l’aide d’un tissu abrasif placé sur un cylindre rotatif. La perte de volume du caoutchouc testé est calculée à partir des mêmes conditions de test que celles pour enlever 200 mg du caoutchouc standard approprié.
Dureté
La résistance de la surface du matériau à la pénétration d’un objet pénétrant de dimension définie sous l'action d’une charge définie. La propriété de dureté est citée dans deux systèmes courants (qui ne sont pas nécessairement corrélés) :
- DIDC (Degré International de Dureté du caoutchouc) - basé sur la mesure de la pénétration d’une balle rigide spécifique dans une éprouvette sous l’action d'une charge permanente définie. Une version réduite de l’instrument de charge permanente est disponible pour effectuer des mesures sur de petites sections transversales et de faibles épaisseurs DIDC « M ».Pour les surfaces courbes, la « dureté apparente » est souvent mentionnée, car les valeurs DIDC et Shore A ont tendance à être plus variables lorsqu’elles sont mesurées sur une petite surface courbe, comme l'illustrent
les joints toriques. - Degrés de dureté Shore – les équipements de test utilisés pour mesurer la dureté sont souvent appelés des duromètres (type A ou D). Les deux utilisent un ressort calibré pour agir sur un pénétrateur défini qui pénètre dans l’éprouvette.Les échelles de dureté sont calibrées en
degrés allant de 0 (infiniment souple) à 100 (extrêmement dur).
Résistance à la chaleur et vieillissement accéléré
Détérioration contrôlée par l’air à haute température et à la pression atmosphérique suite à laquelle les propriétés physiques sont mesurées et comparées avec des éprouvettes non vieillies. Les propriétés typiques mesurées sont les changements de dureté, l’allongement à la rupture, la résistance à la traction et la contrainte sous diverses déformations.La résistance à la chaleur et le vieillissement accéléré sont également liés au « dégazage », où un élastomère, lors d’une exposition initiale à des températures élevées, peut perdre certaines huiles de traitement ou des fragments de faible masse moléculaire du polymère. Dans certaines applications, ces pertes de polymères peuvent interférer avec des composants ou des procédés critiques. Généralement, cette perte de poids peut être mesurée en utilisant l’analyse thermogravimétrique (TGA), souvent associée à d’autres équipements si les constituants spécifiques de la perte de poids ont besoin d’être identifiés.
Résistance à basse température
La résistance à basse température de tout polymère dépend de la température de transition vitreuse du matériau (Tg). Il s'agit de la température à laquelle l’élastomère passe d’un matériau de type caoutchouc à un matériau cassant. Lorsqu’un élastomère se rapproche de sa température de transition vitreuse, on peut anticiper généralement une augmentation de la résistance à la traction, de la dureté, du module et de la déformation permanente à la compression. La Tg pour tout élastomère donné est principalement fonction de la structure du polymère, mais elle peut être légèrement modifiée par l’utilisation d’huiles.Il existe de nombreuses méthodes permettant de déterminer la performance à basse température d’un élastomère. L’analyse calorimétrique différentielle (ACD) est la méthode la plus courante pour évaluer la zone de transition vitreuse. Cette méthode utilise des mesures précises de changements d’enthalpie des matériaux sur une plage donnée de température. L’analyse de ces données permet de mesurer précisément la transition vitreuse.D’autres tests se concentrent sur des paramètres plus physiques. Par exemple, le test de rétractation à la température (TR) consiste à immerger une éprouvette étirée standard dans un bain à -70°C jusqu’à ce qu’elle devienne rigide, permettant ainsi à l’échantillon de se rétracter librement et d’élever la température de 1°C/min. La température à laquelle l’éprouvette s’est rétractée de 10 % de l’étirement d’origine est appelée « TR10 ». Une valeur ajoutée à TR10 définit l’étirement initial, par exemple le test TR10/50 étire l’échantillon de 50 %.
Une méthode alternative pour décrire la rigidité à basse température d’un élastomère consiste à utiliser le test Gehman (ISO1432 : 1998). Cette méthode de test mesure le module d’élasticité en torsion d’une éprouvette standard à différentes températures.Les valeurs du module relatives aux températures mesurées sont déterminées (le module relatif à une température donnée est le rapport entre le module d’élasticité en torsion à cette température et le module d’élasticité en torsion à 23 °C). La température à laquelle le module relatif est égal à 10 est appelée T10, celle à laquelle le module est égal à 5 est appelée T5, etc.
Dégazage
Le dégagement de gaz à partir d’un matériau ou de portions du matériau de faible poids moléculaire. Ces gaz, ainsi que les gaz à la surface
du solide, peuvent être libérés dans un environnement sous vide pour former une fuite perceptible. À température ambiante, les substances dégazées prédominantes sont de la vapeur d’eau et des hydrocarbures. Le taux de dégazage augmente à des températures plus élevées, ce qui augmente le taux de perméabilité et peut initier des réactions chimiques dans l’élastomère qui libèrent d’autres gaz. Les substances dégazées peuvent se condenser sur les surfaces ou réagir avec des produits chimiques du procédé, ce qui peut inhiber les performances.
Perméabilité
La perméabilité de gaz ou vapeurs à travers l’élastomère. C’est une propriété importante si l’élastomère est utilisé pour éviter les fuites de gaz ou de vapeurs de compartiments, etc. Le taux de perméabilité dépend du type d’élastomère utilisé et de la composition du composé final (type de charge, plastifiants, etc.). Le degré de perméabilité se réduit généralement à partir des élastomères silicone (le plus élevé), suivis par NR, EPDM, SBR, CR, NBR, FKM et FFKM, ECO et IIR.
Polymérisation au peroxyde ou au soufre
Plusieurs mécanismes de réticulation (polymérisation) peuvent être utilisés pour les différents types d’élastomères, parmi lesquels on trouve les systèmes polymérisés au soufre et les systèmes polymérisés au peroxyde. En général, les systèmes polymérisés au soufre présentent de meilleures propriétés mécaniques d’origine, mais les pires propriétés de vieillissement thermique et vice-versa pour les systèmes polymérisés au peroxyde.
Pression
L'ampleur de la déformation appliquée au joint torique ou au joint exprimée en pourcentage de la section transversale d’origine. La déformation du joint torique entre des matériels d’accouplement crée un joint efficace. C’est l’élasticité du caoutchouc qui fait que la force d’étanchéité « repousse » contre les surfaces de contact.L’augmentation de la pression augmente la force de charge de compression générée par le joint, cela peut potentiellement endommager ou déformer les matériels d’accouplement. La déformation rémanente après compression réduit l’amplitude de la force d’étanchéité exercée par le joint torique au fil du temps.
Étirement
Pour fournir une étanchéité efficace, le diamètre intérieur (DI) du joint torique doit être plus petit que le diamètre de la gorge du piston. Cela garantit un léger étirement du joint torique, ce qui fait qu’il s’adapte bien à la gorge. L’étirement idéal se situe entre 1 % et 5 %, 2 % étant considéré comme la valeur optimale dans la plupart des applications. Un étirement supérieur à 5 % n’est pas recommandé car cela réduit la section transversale et peut augmenter la contrainte sur le joint torique, provoquant ainsi un vieillissement accéléré.
Propriété de traction
Un essai simple sur des éprouvettes d’élastomères en traction est couramment utilisé pour définir la résistance des matériaux. La représentation la plus courante se fait sous la forme d’une courbe contrainte-déformation technique ; la contrainte-déformation technique se base sur les dimensions d’origine pour les calculs, par opposition aux dimensions réelles pendant l’essai (la section transversale ne reste pas nécessairement constante pendant l’essai). Une courbe typique contrainte-déformation technique d’un test de traction est présentée ci-contre.
Ϭ = Contrainte technique.
ε = Déformation ou allongement technique rapporté comme un pourcentage de la longueur testée d’origine.
- Contrainte de traction (R)
La contrainte appliquée pour allonger l’éprouvette, calculée comme la force par unité d’aire de la section transversale initiale de la longueur testée. Les résultats sont normalement donnés en MPa. - Allongement (e) - L’allongement exprimé en pourcentage de la longueur testée initiale, produit sur l’éprouvette par une contrainte de traction, c’est ce qu’on appelle le pourcentage de déformation.
- Résistance à la traction (Re) - La contrainte de traction maximale enregistrée lors de l’étirement de l’éprouvette jusqu’au point de rupture. Également décrite comme étant la « contrainte de traction ultime ».
- Résistance à la traction à la rupture (Rm) - La contrainte de traction enregistrée au moment de la rupture de l’éprouvette.
Remarque : les valeurs de Rm et Re peuvent être différentes si, après le seuil de plasticité, l’élongation se poursuit et est accompagnée d’une chute de la contrainte, ce qui fait que Re est inférieure à Rm. - Allongement à la rupture (A%) - Allongement (exprimé comme un pourcentage de la longueur initiale) au point de rupture.
- Allongement à une contrainte donnée (e) - Allongement en traction dans la longueur de test lorsque l’éprouvette est soumise à une contrainte de traction donnée.
- Module ou « Contrainte à un allongement donné » (Et) - La contrainte de traction dans la longueur testée à un allongement donné. Cette définition est largement utilisée avec le terme « module » et il faut veiller à éviter toute confusion avec d’autres utilisations du terme module, telles que le Module de Young, qui correspond à la pente de la courbe linéaire contrainte-allongement. Ni le module de Young ni le module sécant ne sont applicables aux matériaux non linéaires et ne sont donc pas utilisés pour les élastomères.
- Densité d’énergie de déformation (W) - définie comme étant le « travail accompli » pour une contrainte donnée, c.-à-d. l’aire située sous la courbe contrainte-déformation après un allongement défini.
Résistance au déchirement
Force médiane nécessaire pour propager une coupure dans une éprouvette ayant la forme d’un « pantalon », divisée au niveau de l’épaisseur de l’éprouvette.Le terme indique la résistance à la propagation d’une petite découpe faite au préalable dans un élastomère. Le test le plus courant utilise la méthode de résistance au déchirement (ASTM D624, Die T), avec une éprouvette ayant une forme de pantalon.
Tolérances
Valeur de la variation permise sur les dimensions et les surfaces pendant le procédé de fabrication. La tolérance est égale à la différence entre les limites maximales et minimales d’une dimension spécifiée. Comme les métaux sont durs et qu’une interférence peut empêcher l’assemblage, elles sont généralement tolérées et considérées comme étant un ajustement. Les alésages sont définis par une dimension plus une variation admissible. Les arbres sont définis par une dimension moins une variation admissible. Comme les pièces en élastomère, telles que les joints toriques, sont flexibles et sont généralement conçues pour être soumises à des interférences (compression ou tension), leur diamètre et leur section transversale sont généralement indiqués avec une tolérance ±.
Les tolérances des joints toriques pour chaque dimension normalisée sont données dans le tableau Dimensions des joints toriques .
Nous vous recommandons d’utiliser la norme ISO3302-1 Classe M2, X2 dans la conception de composants en élastomère sur mesure.
Modification du volume
Le degré de dilatation ou de contraction d’un matériau lors de son exposition à des environnements opérationnels est un facteur important à prendre en compte dans toute application d’étanchéité. Les fluides industriels peuvent être absorbés par le matériau provoquant son gonflement. Les fluides industriels peuvent également éliminer par lessivage des ingrédients contenus dans le matériau entraînant ainsi une diminution du volume ; parfois les deux phénomènes peuvent se produire, un gonflement initial suivi d’une contraction. Certains environnements à haute température et chimiques peuvent provoquer un resserrement de la structure réticulée, entraînant ainsi une diminution du volume.Les mesures de volume avant et après exposition sont exprimées comme une variation en pourcentage.
Résistance à l’érosion, à l’ozone et aux UV
Une exposition d’élastomère à l’usure peut entraîner une détérioration du produit due principalement aux effets de la lumière du soleil, en particulier la composante UV (ultra-violet) du spectre lumineux. La lumière UV a un effet sur la scission de la chaîne polymère principale, conduisant à une dégradation rapide de l’élastomère. Cette dégradation se manifeste sous la forme de fissures en surface souvent appelées craquelures et peut laisser pénétrer l’eau qui lessive les composants solubles et qui conduit à la rupture du joint. Cette forme d’attaque est plus connue dans les matériaux qui présentent une insaturation (double liaison carbone-carbone) au niveau du squelette du polymère et elle est accélérée par les contraintes exercées sur le matériau (attaque chimique induite par la contrainte). Pour faire face à la situation, des stabilisants chimiques UV peuvent être incorporés à la formulation : le noir de carbone est généralement reconnu comme étant un des systèmes de protection contre les UV les plus efficaces à utiliser pour les élastomères.De même, l’ozone (un oxydant puissant) peut dégrader des composants en élastomère de la même manière que les UV. L’utilisation d’un antioxydant et le choix judicieux des élastomères (polymères saturés) peuvent réduire ou éliminer de manière significative ce problème.